Lithuanian Weaving, Fabric Weaving Maker Project, The Bees Are Buzzing, AQS QuiltWeek Paducah
- Heidi Proffetty
- May 7, 2022
- 10 min read
I think it’s safe to say that the inspiration for my latest sewing project came straight from one of my newest crafts, weaving. I am sure that anyone who has seen my Moroccan Mosaic quilt designs, can appreciate why I would find the colorful geometric patterns of weaving so appealing.

Lithuanian Colorful, Geometric Patterned Sashes
Over the past 2 years, I have been learning about this craft and its history from a dear Lithuanian friend of mine. She teaches weaving and about Lithuanian culture in the Boston area. Not only does she excel at her craft but she finds the importance of keeping its heritage and traditions alive through her teachings.


Danute Mileika & Heidi Proffetty
My friend grew up in Lithuania and remembers her mother spinning fibers and although flax was no longer grown in the area where she lived, her mother would often share her stories of growing and processing flax as a child.

Flax plant in bloom. The beautiful blue blooms only last one day.
Today, she still has her mother’s beautiful wooden spinning wheel as well as several other 19th century spinning wheels and various looms that she uses and displays at teaching events and in her home. In fact, it is not uncommon to find linen throughout each room of her house from beautifully woven sashes, table linens, scarves, and rugs to baskets and vessels filled with bundles of dried flax. Every year she grows small amounts of flax in her yard not only because she enjoys working with the natural fibers but it gives her ability to fully teach others about the entire cycle of processing flax from seed to linen.

19th Century Spinning Wheels from Danute Mileika's personal collection.
Linen cloth is naturally made from the fibers of the flax plant and in Lithuania is used to make garments, celebratory sashes, table cloths, napkins and bedding. The flax or linseed was grown on farms cultivated through a multi-step process which was mostly done by the women. The long fibers inside the stem’s inner core were extracted through a process called retting or breaking the flax, the fibers were then combed to clean any remaining debris and afterward, spun into yarn using a spinning wheel. The resulting fibers would later be woven into linen cloth. The importance of linen was also intertwined in Lithuanian folk songs, dances and celebrations. Over the years, as inexpensive fabrics became more readily available and cultivating flax became less profitable along with the use of automated weaving machines and with many of the younger generation never touching a loom, both the craft and its history seemed to be facing an end. However, certified Lithuanian artisans, passionate teachers such as my friend and other weaving enthusiasts are sharing and keeping the craft as well as its history alive. The photos are from my friend's personal collection.

Linen examples from Danute Mileika personal collection.

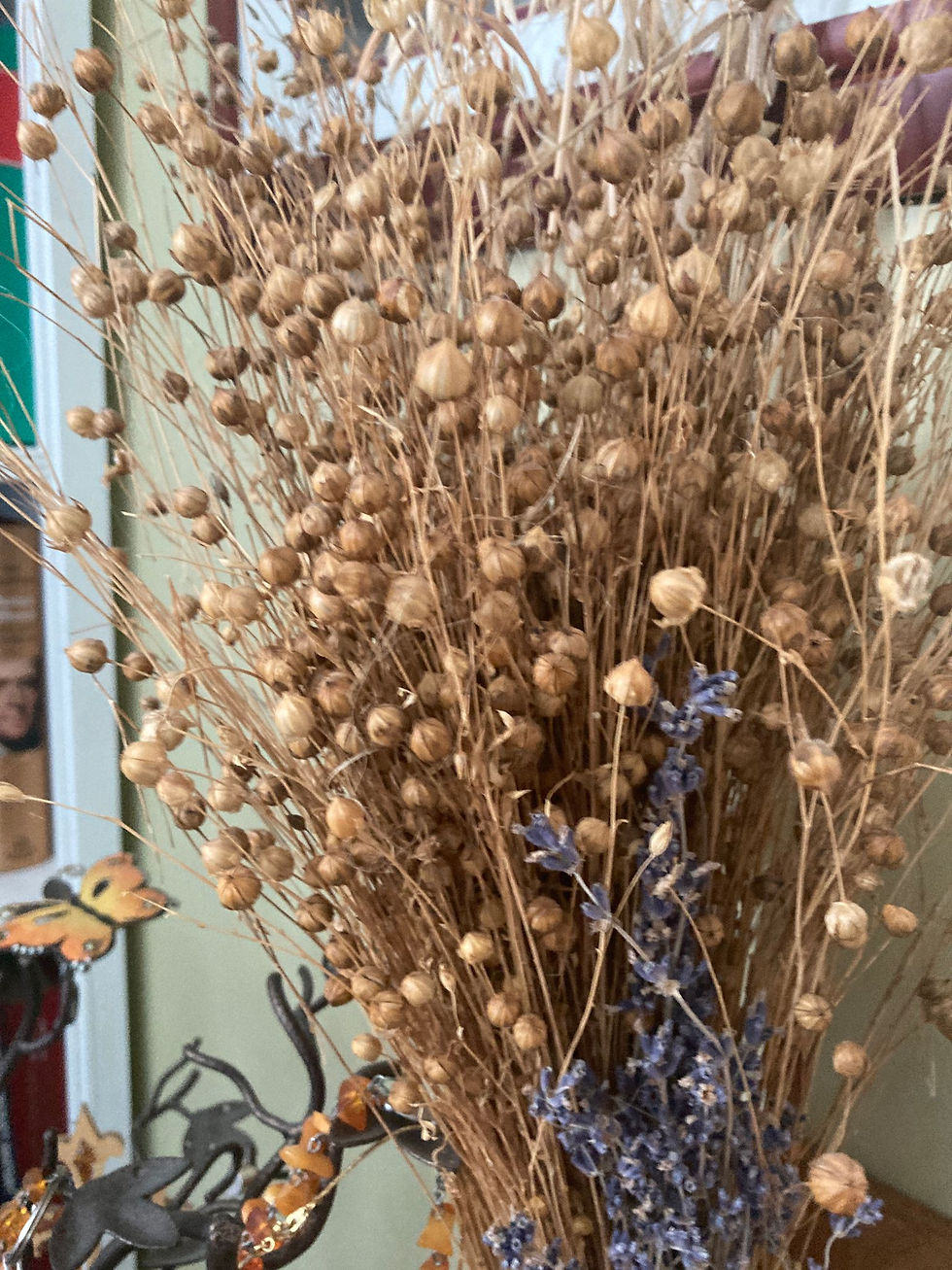

Interested in learning how to weave, my friend suggested that one of the simplest ways to start, was to weave on a rigid heddle loom. My Rigid Heddle Loom pictured below is from the Ashford Wheels & Loom Company. The loom is made of beechwood, it's compact and portable, comes with or without a stand option, it's easy to use and is a good loom for both beginners and experienced weavers.

The easiest weave pattern and one that most first choose to experiment with, is what’s referred to as a simple or plain weave. Plain weave is the most common type of basic weave pattern in which the yarn passes over and under warp yarns and then repeats the same pattern with alternate yarns in the following row which produces a checkered appearance. Here’s what it looks like.

I'm sure just like any other weaver does, I love to watch the weave pattern as it develops. Below, I am weaving a hounds tooth pattern or design. This pattern looks similar to a plain weave with alternating blocks of color producing that familiar checkered board design.

I find that weaving, is a very quiet craft and depending on the pattern, such as this hounds tooth design, it can also be repetitive, meaning it not easy to lose track of the design and doesn't really require a lot of concentration. Weaving this type of simple pattern, can easily allow your mind to wonder or drift off to other things. I think this is the main reason why I was inspired to try the following technique, fabric weaving using my sewing machine. I had seen fabric weaving projects in the past but I had never really played with the technique.
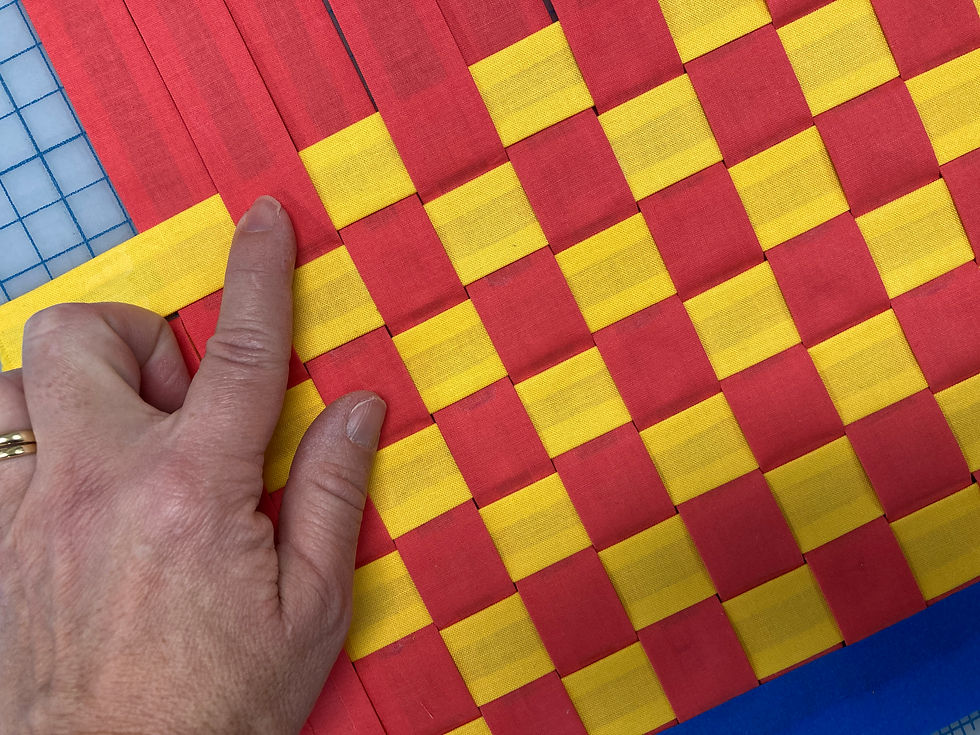
Basically, fabric weaving, is weaving strips of fabric together like you did when you were a child but out of strips of construction paper instead of fabric. I wanted to try fabric weaving for myself and to eventually make and share a sewing project that incorporated the technique. And that is exactly what I did. Using a plain weave design and some long sewing machine stitches to embellish my project, I created the following fun weaving & sewing project, called Fiesta Weave Lunch Mats.

Nothing say’s bring on the party more than with these brightly colored, fabric woven lunch mats. All that’s needed to make your own set of 4 mats, are a few basic sewing supplies, follow some easy steps to create a simple plain fabric weave pattern and a few tips to finish your mats with decorative straight stitches and neat mitered corners. Make a set for your upcoming celebrations or use them anytime to jazz up your table. Set down these colorful woven mats, grab a vase of fresh blooms and plate up your favorite lunch or snack. You and your guests will definitely be feeling the urge to fiesta! Visit Janome’s project page here or click on my website link here both will take you directly to the steps to make this project.

Fiesta Weave Lunch Mats by Heidi Proffetty
www.heidiproffetty.com
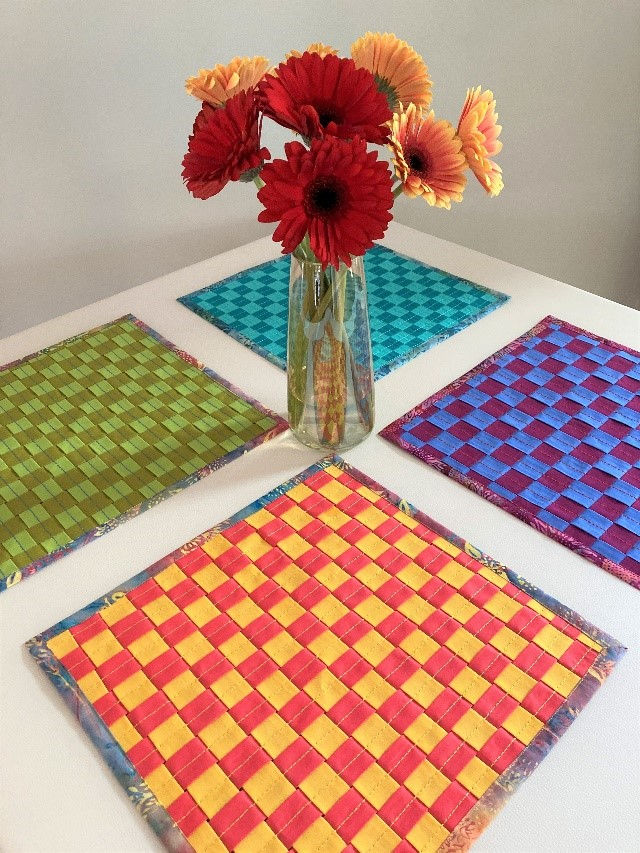

This spring marks our 5th season as beekeepers. I remember our mentor telling us that it takes at least 5 years to become good at beekeeping. He was not wrong. There is much to learn and to appreciate about this hobby. As we prepared to do our spring inspection, we found that both of our hives did not survive the winter. There are any number of possible reasons why our hives failed: beekeeping inexperience, a weak hive colony going into the fall season, diseases from varroa mites or pesticides, hive damage from other pests seeking shelter and reeking havoc once in the hive, starvation or lack of food, improper ventilation or excess moisture issues. Sadly, pictured below, is a queen bee from one of our winter hives, she and her winter worker bees did not make it to spring. Typically, queen bees can live up to 2 1/2 years if a hive survives the winter.
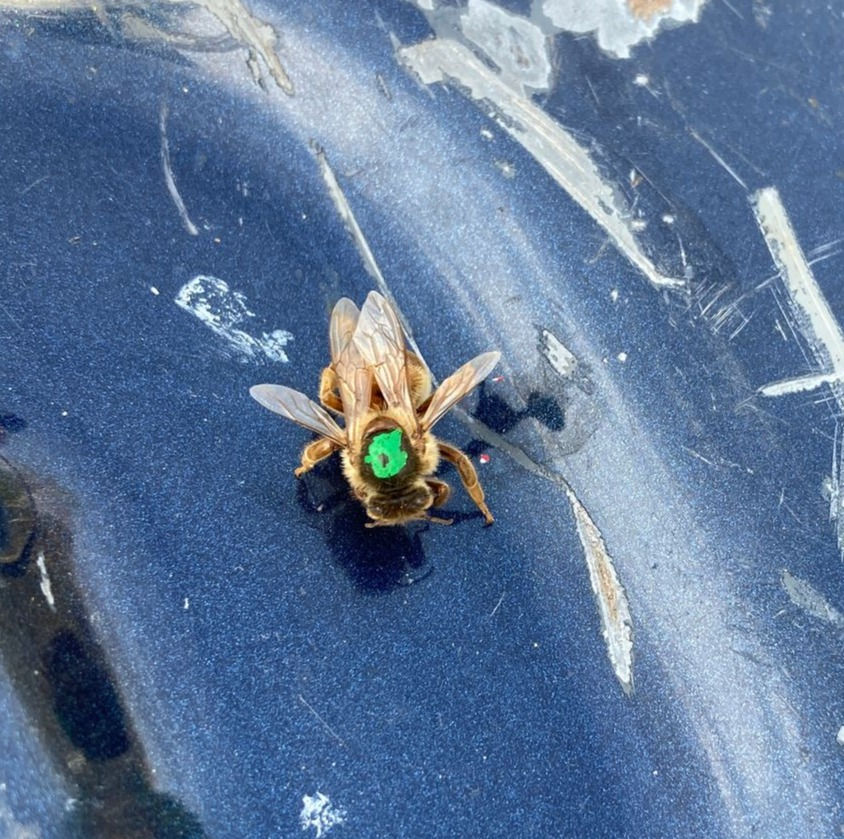
During the winter, when temperatures fall, honeybees do not go outside the hive to forage, nor do they don’t hibernate and the queen does not lay eggs. The only job the winter bees have is to protect the queen until spring arrives when she will start to lay eggs once again. As the temperatures grow colder, the bees cluster around the queen, the colder it gets, the tighter the cluster becomes in an attempt to increase the hives temperature and keep the queen warm. The bees rely on their honey stores. Honey stores are honey that has been encased in the comb and capped by the bee during the late summer into fall. They make honey as their own food source. Our typically winter season is longer than most and therefore our bees would require upwards of 60 lbs of honey to make it through. The bees eat the honey to give them the energy that they need to accomplish the task of keeping the queen bee and hive warm. This is why it is important to check in the late fall and throughout the winter that there is ample honey stored in each hive so that bees don't die from starvation. As I mentioned earlier, in the northeast, where the winters are longer, more food is needed so sometimes it is necessary to provide supplemental food such as fondant.
As a result of losing our bee colonies and of course still wanting to continue our beekeeping hobby, we ordered two new packages of bees through our local beekeeping association. A single package of bees weighs roughly 3 lbs. and contains around 10,000 honeybees plus 1 queen bee.

Our bees came from commercial apiary in Georgia and they arrived in the middle of the night at one of the association member's homes just before my trip to teach at QuiltWeek in Paducah, KY.

This is a photo taken the next morning of the stacks of bee packages waiting for many local beekeepers who were eagerly standing in line bright and early to pick up their bee packages.

Here you can see my husband and I preparing to install our new bees. First, we must take care of the queen bee. She is in her own separate cage, called a queen cage. This queen cage is attached to a frame which will then be placed in the hive.
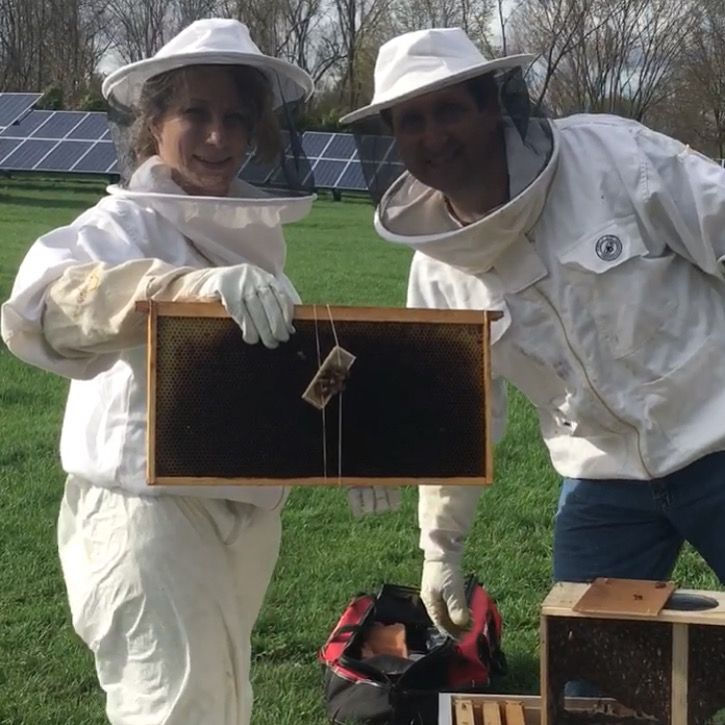
She will remain in this small wooden box with a screen and few attendants, attached to a frame using rubber bands for about 3-7 days. During this timeframe, the remaining 10,000 worker bees who have now also have been installed into the hive and rooming around freely, can chew through a candy cork on the end of the cage thus releasing her.

Since we are seasoned beekeepers and already have honeycomb built out on our existing frames by our previous bees, the queen bee can very quickly start laying eggs. A typical queen bee can lay from 800 to 2,000 bees per day. She does not have to wait for the worker bees to build new honeycomb which takes both time and resources. For our new bees, it's like moving into an already furnished home. The purpose of the queen cage procedure is to allow her fellow workers bees ample time to accept her. They smell her pheromones and begin to recognize her so they won’t think that she is a predator and try to kill her.
About a week after our bees are installed, it is normal procedure to check to make sure the queen bee is out of her cage and to remove the empty queen cage from the frame. When I returned from my trip, I headed out to my hives to do just that. It wasn't the best weather to be tending our hives but it was important for me to know that both queens were free. Pictured here you can see that I am checking to make sure the queen is out safety and to remove the empty cage. As a matter of fact, upon inspection of our second hive, I actually spotted the queen, she easily recognizable because she is marked with a green dot. She was walking around on the frame containing the empty queen cage. I quickly put the frame back and closed the hive as to not disrupt her. Now, we will leave the hives alone for additional week before we take another peek.

Almost one year ago, I was feeling very hopeful and excited as I returned my signed contract to teach for the first time at an AQS QuiltWeek show. I had been originally invited to teach at the 2020 AQS QuiltWeek Paducah show but unfortunately, the show was cancelled all together as the world was dealing with Covid.

Flash forward to April 2022, it had now been almost 2 ½ years since I had last taught in person anywhere, let alone to be teaching at a new venue with a staff I have never worked with before, a convention center that I wasn’t familiar with, a full schedule including 4 classes and 1 lecture, and added to the mix that I was preparing to teach 2 entirely new class offerings on creating stitch art designs which involved some serious preplanning on my part. Sewing machine classes require extra due diligence when preparing to teach.

Decorative Stitch Art Designs by Heidi Proffetty
The focus of my 2 new stitch art classes were not only on using sewing machine stitches to create unique stitch art designs but also to teach students how to be more comfortable using there sewing machines to make these designs. How to make stitch adjustments such as changing the width and length stitch and using features like elongation, tapering, flipping, and programming stitch pattern combinations. Students in my classes were working with the Janome 8200 QCP SE, a well-built, mid-level computerized sewing machine offering 170 stitches to play with and other robust features. Since many of my students had not sewn on the Janome 8200 QCP SE before, the real test came, on how quick and comfortable I could make them feel in maneuvering around these sewing machines to access all the wonderful other features outside of stitch adjustments that computerized sewing machines have. So, you can probably imagine the bundle of emotions that I was feeling as I stepped off the plane in Paducah. But I came prepared to teach, I was excited to share and I was thrilled to be in the good company of my students, colleagues and friends.
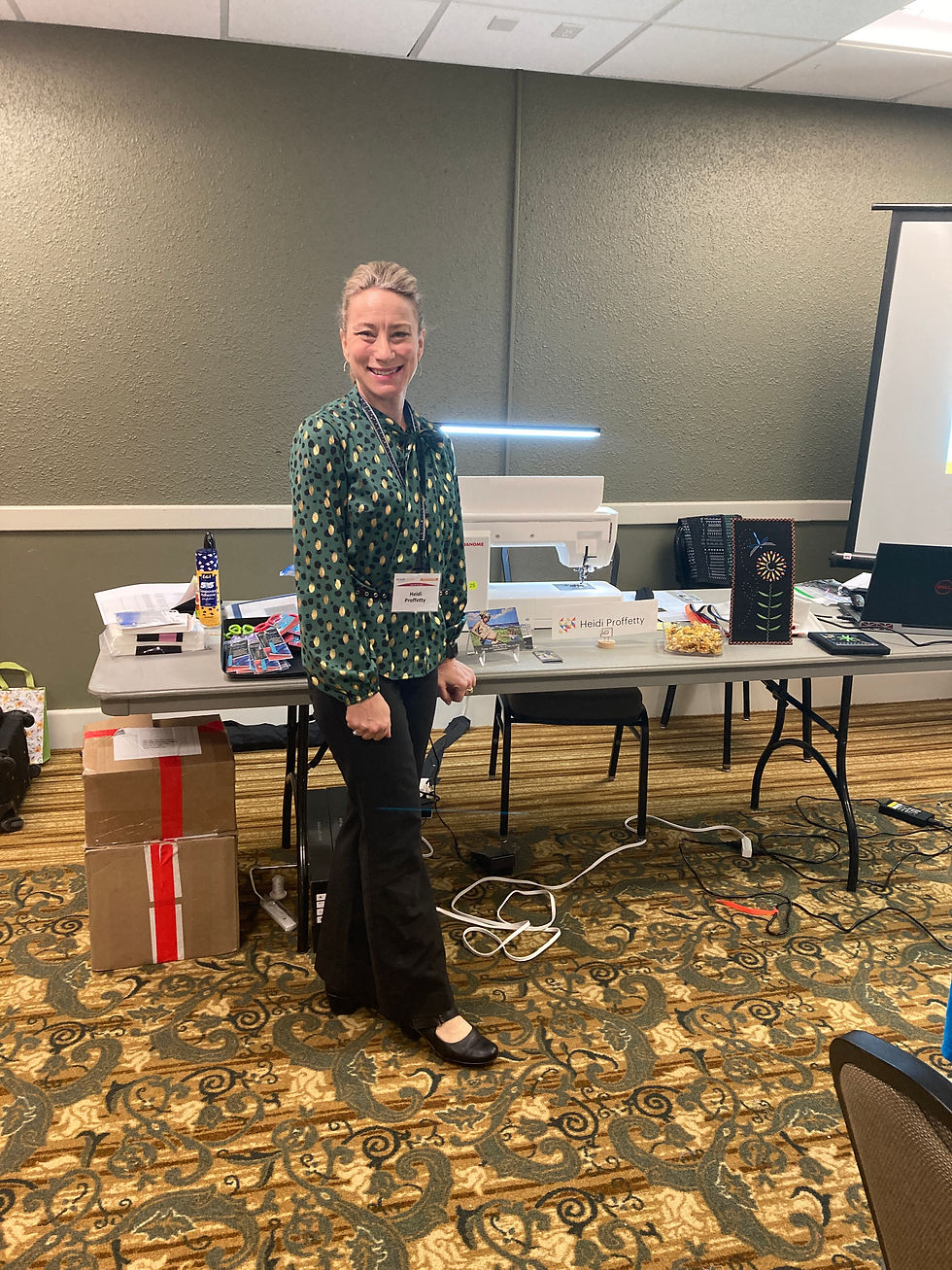
I am pleased to tell you, that my first teaching event an AQS QuiltWeek Paducah was a terrific success. All of my classes were filled and my students came ready to learn, they were engaged throughout my classes and fun to be with. The AQS staff was prepared too. In my opinion, they were organized, professional, friendly and accommodating when needed.
I had a few added bonuses during my stay in Paducah, while in attendance at the 36th annual awards ceremony, I had the privilege of receiving a first-place category recognition for one of my Moroccan Mosaic quilts, Azul Medallions. It was a very proud moment to be recognized for my talent amongst many other very talented and gifted peers and quilt makers.

SMALL WALL QUILTS: Movable Machine Quilted sponsored by Pro-Stitcher
1st Place: #1208 AZUL MEDALLIONS by Heidi Proffetty of Bridgewater, MA
I also had the pleasure of enjoying a few fun get togethers, lunches and dinners with both old and new friends and in-between teaching, I got to visit some of my favorite vendors and of course looked at the quilts! You can see the some of the winning and extraordinary quilts here on the AQS Website. These meet ups were long overdue and appreciated more than words can say. And lucky for me, due to some unforeseen flight delays, my trip was extended past the show. So, a few very kind and local friends made sure that I wasn’t stuck in my hotel room and saw to it that I was able to see a little more of Paducah. We visited the quilt museum, some local artisan shops, hit the coffee shop, walked the riverfront and ate more yummy foods at other local eateries.

National Quilt Museum, Heidi Proffetty, Rosemarie Steele & Laura Hendrickson in front of
Karen Kay Buckley's quilt, Fiesta Mexico.
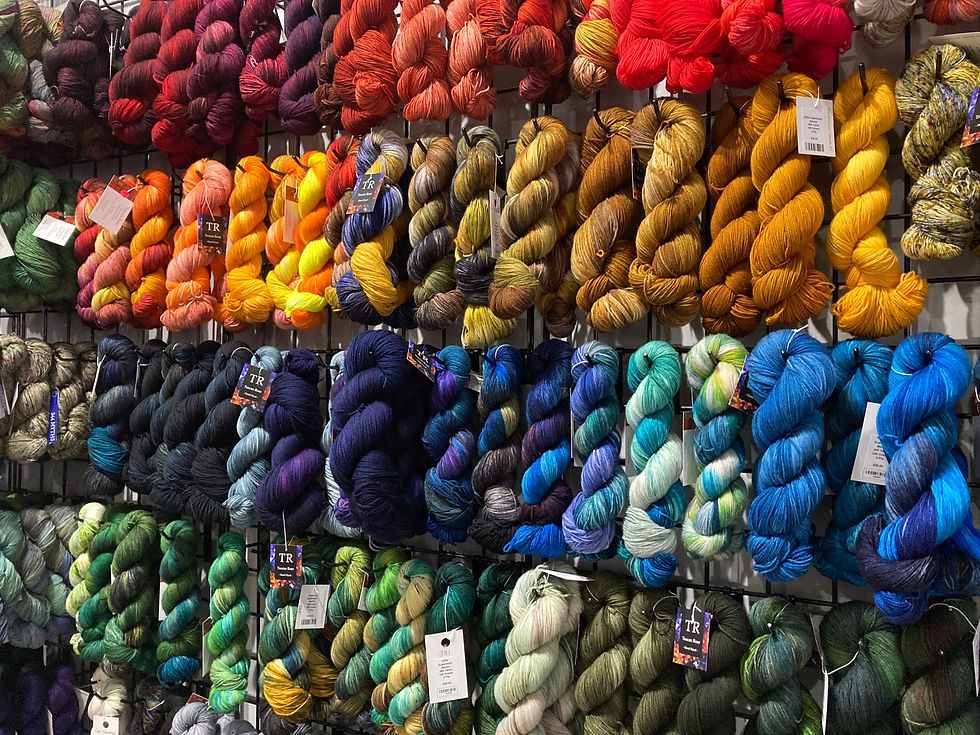
Patty Van Dorin owner of Tuscan Rose in Paducah, KY. Hand-dyed yarns and fabrics.
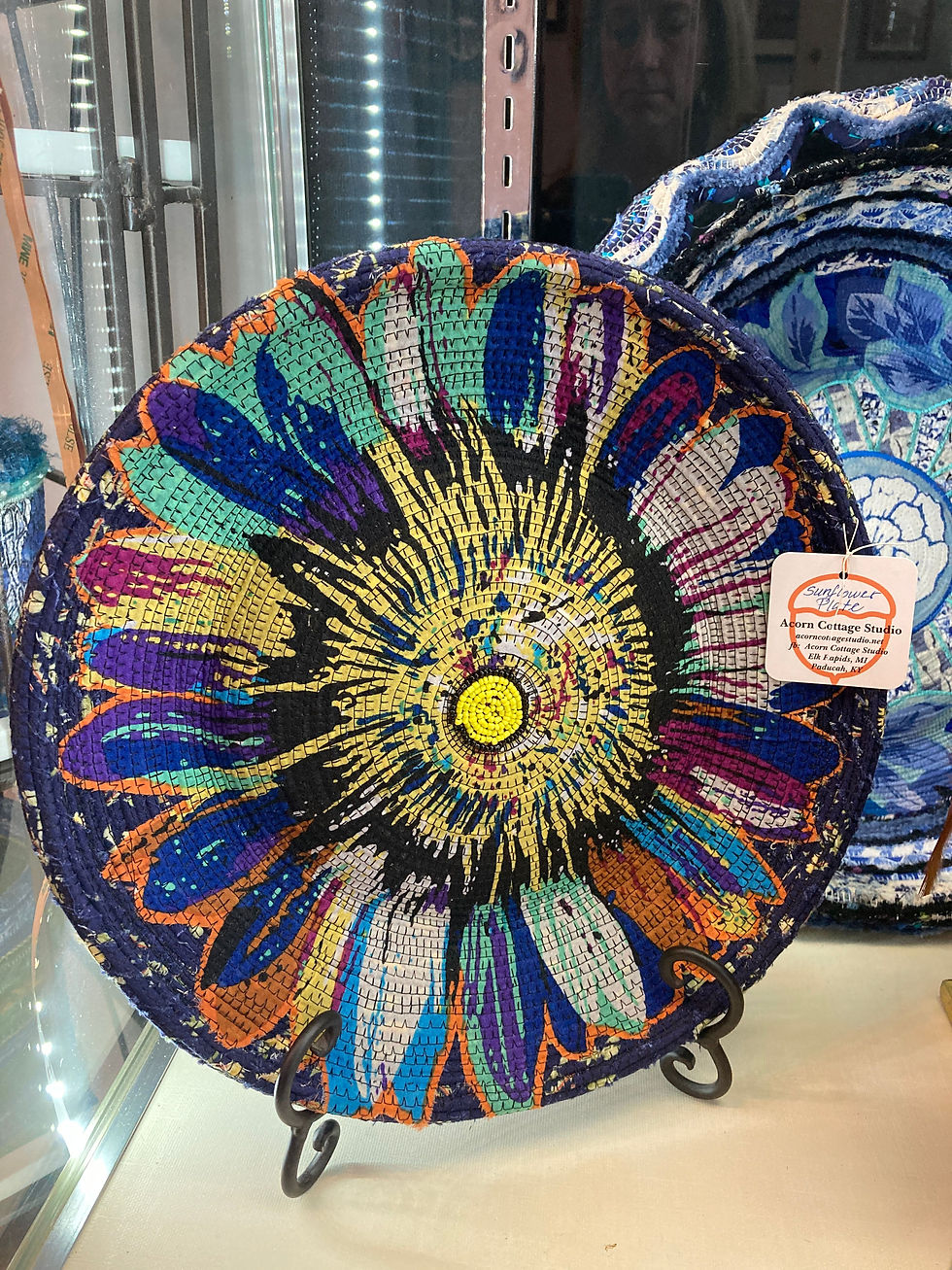
The Art Guild of Paducah. Featured Artist, Kerry Bowes. Painted Fiber Art Rope Bowls.
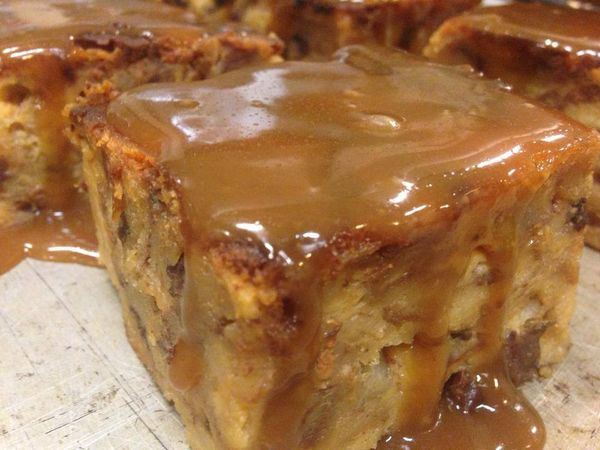
Kirchhoff's Bakery, Paducah, KY. Bread Pudding with Carmel Sauce. Courtesy of some wonderful new friends!
Thanks for sharing the love of quilting and sewing with me!
Comments